準交監控貫穿物料/工單/MES,訂單出貨平均縮短16天, 在製成本降低32% 機械設備或汽車零組件等相關產業,因為產品工序製程繁複,製造週期經常跨日甚至跨週,中途容易發生各種無預警的障礙、停等或移轉等狀況,造成生產時程拉長或不順暢,除了可能耽誤交期,也會間接增加在製庫存成本,影響整體利潤。
本案例客戶為自動化機械設備設計製造商,營業範圍包含自行車相關整廠設備、醫材設備、各式管類加工設備等,導入MES是希望能夠達成準時派工、開工生產、進一步滿足準交需求,但因為每個產品45道製程起跳、單一廠區擁有61個機台、每天會運作22小時,生產明細資訊量龐大,無法立即統計實際加工時數,依賴專人整理報表費工又不即時,難以深入掌握生產段未達標的原因,故以BI整合MES與ERP,自動派送生管人員需要的重點分析,將各工作站生產資訊如:工單是否發放、各批次目前狀態(待進站、生產中、良品倉等)、各批次進出站時間、前一站出站時間、各批在製量等內容,彙總成有衡量價值的各種指標依據,有效解決以下滯礙:
一、派工憑個人經驗,製程需要多個部門協作,溝通容易出現落差
BI自動彙總各批號的總生產時間、每段生產時間,讓管理者判斷個別產品生產時程的合理性,檢視生產狀況是否符合預估:負毛利時,則調閱報工異常;交期延遲,分析是那個製程停等最久(由報表往下查看明細);並統計物料停等的時間,進而控制在製庫存成本。
二、資訊不即時,無法預估接下來的人力物力與生產力,更難以改善製程缺口
生管藉由BI理解當下生產狀況,依照生產數量和標準工時,來計算還有多少產出和工時需消耗,幾乎可預估兩三天後的產能與工料,協助判斷各區是否要外包或加班,;再由各工序報表得知停等最久的程序是哪個?等多久?原因為何?有改善的空間嗎?例如搬運次數過多,就有可能是路徑未優化,若進一步調整設備間的布局,便能縮短虛耗。
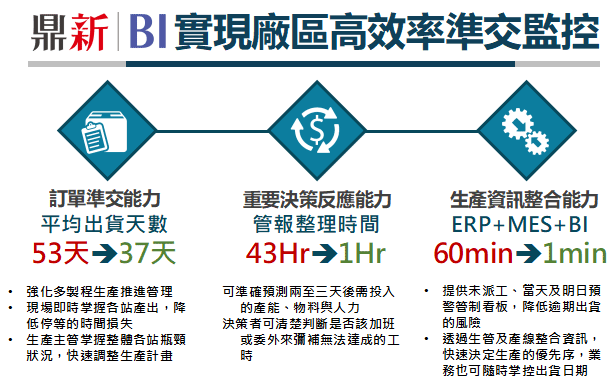
未派工、當天及明日預警管制看板
針對小批量生產設計,可迅速掌握大量工單---有哪些已經延遲 ? 又哪些單子需要接著準備
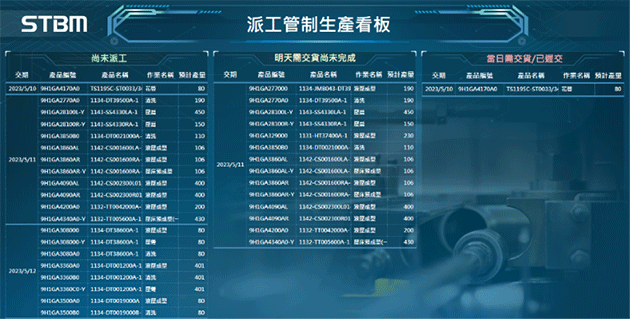
重要製程生產看板
打通關鍵製程的生產資訊,讓現場主管快速掌握各站狀況,降低停等的時間損失
需求與產能控制看板
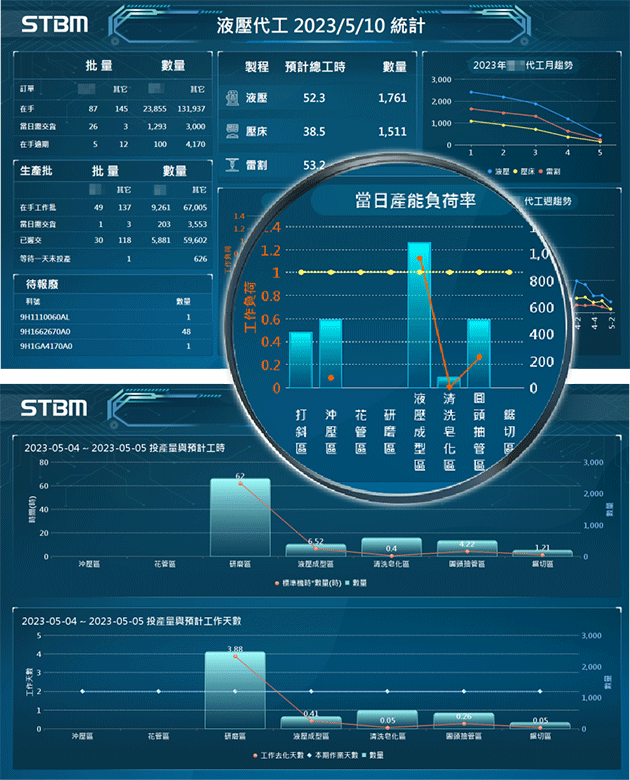
- 完整掌握在手訂單、逾期數量,同時監控關鍵製程的生產批量,待進站數量
- 能更快速評估調節內部工作及外包計畫,儘可能滿足交期的同時,也將內部產能發揮至極大化
|